Climbers tend to be an ecologically sensitive group. But they clamber on constantly changing routes in climbing gyms, potentially unconcerned about the sustainability of the thousands of polyurethane or polyester holds. Sadly, especially in North America, most of these holds end up in the dumpster after the texture wears off.
Although climbing hold recycling programs at rock gyms in the United States are nonexistent, the French are well on their way to creating a circular life cycle for climbing holds in large gym chains. Laws mandating the reduction or elimination of plastics apply to these gyms, and climbing hold manufacturers provide financial incentives and infrastructure to make recyclable climbing holds a reality.
According to an article in the Climbing Business Journal, France threw out 7 million climbing holds in 2022. (The United States has over 600 indoor climbing gyms compared to France’s estimated 193.) That same year, the country enacted a law that mandates reducing and eliminating plastics.
The “anti-waste law for a circular economy” addresses everything from single-use plastics and packaging to requiring a plastic microfiber filter on washing machines. Of course, this law includes artificial climbing holds.
Here in the U.S., the adoption of recyclable climbing grips has lagged behind Europe. Trango Holds and Kilter are among the few American brands offering more sustainable holds. Read on for a review of the past, present, and potential future of improving the sustainability of indoor gym climbing.
Standard Climbing Hold Manufacturing
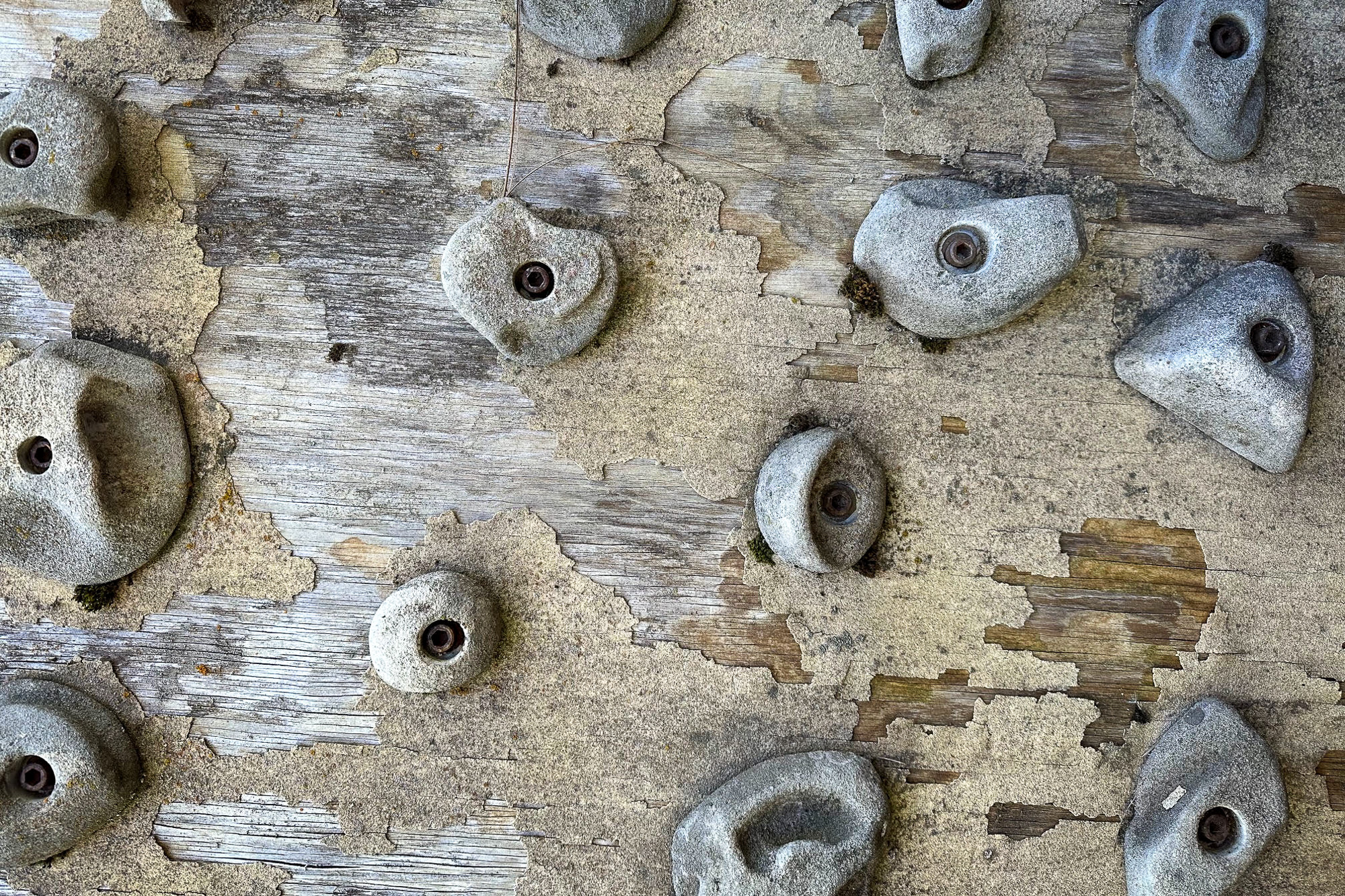
Entre Prises produced the first artificial climbing hold in 1983. Holds were “shaped” out of clay, and then the hardened clay was painted with resin. Some holds were carved natural stones or fired clay. These holds were rather archaic and painful to the skin, but there were no other choices for artificial climbing holds.
The next step in the manufacturing evolution of climbing holds, which still dominates the industry, was “pouring” climbing holds. A shaper created the hold shape from foam and then made a silicone mold around it.
Polyester resin (PE) was poured into these molds and cured. The resin vapors were toxic, and the holds were heavy and chipped easily. However, these polyester resin holds had a desirable texture, were easy to work with, and the material cost was relatively inexpensive. Again, Europe led the way.
In 1985, Metolius Climbing poured the first PE artificial “holds” in the United States. There were no climbing gyms in the U.S., so the market for holds didn’t exist yet. However, the demand for hangboards to train at home was just beginning, so the brand offered its “Simulator” hangboard before making holds a year later.
Polyurethane (PU) burst onto the climbing hold scene in 1991, and hold companies improved the mixtures to create an extremely durable and much lighter hold. PU holds also have some flexibility, unlike their PE counterparts, which allows them to be used on curved or featured walls. They are also much more resistant to chipping.
PU’s higher strength-to-weight ratio allows manufacturers to produce hollow holds, drastically reducing the amount of plastic used. These “hollow-back” holds also reduce shipping costs. These holds still dominate the walls of most climbing gyms.
The foam used to shape the mold contributes to the specific texture of the holds. Hold shapers used styrofoam and surfboard foam but eventually settled on high-density carving foam. Carving foam comes in various densities, allowing shapers to mimic natural textures or create their own.
The Next Step: Recyclable Climbing Holds
According to Climbing Business Journal, the first recyclable climbing hold was produced by Finland’s Greengrip Oy, which started making 100% recyclable climbing holds in 2006.
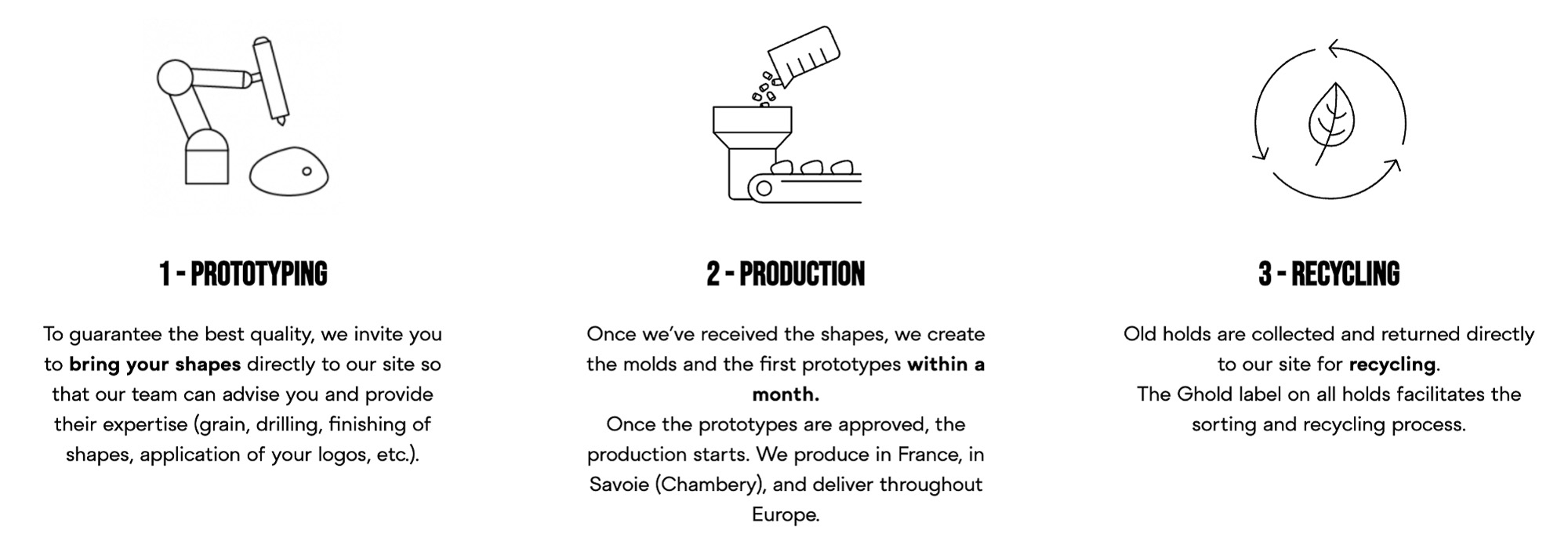
The Final Step: French Circular Climbing Hold Life Cycle

Back in the States: Trango Holds ABS Line
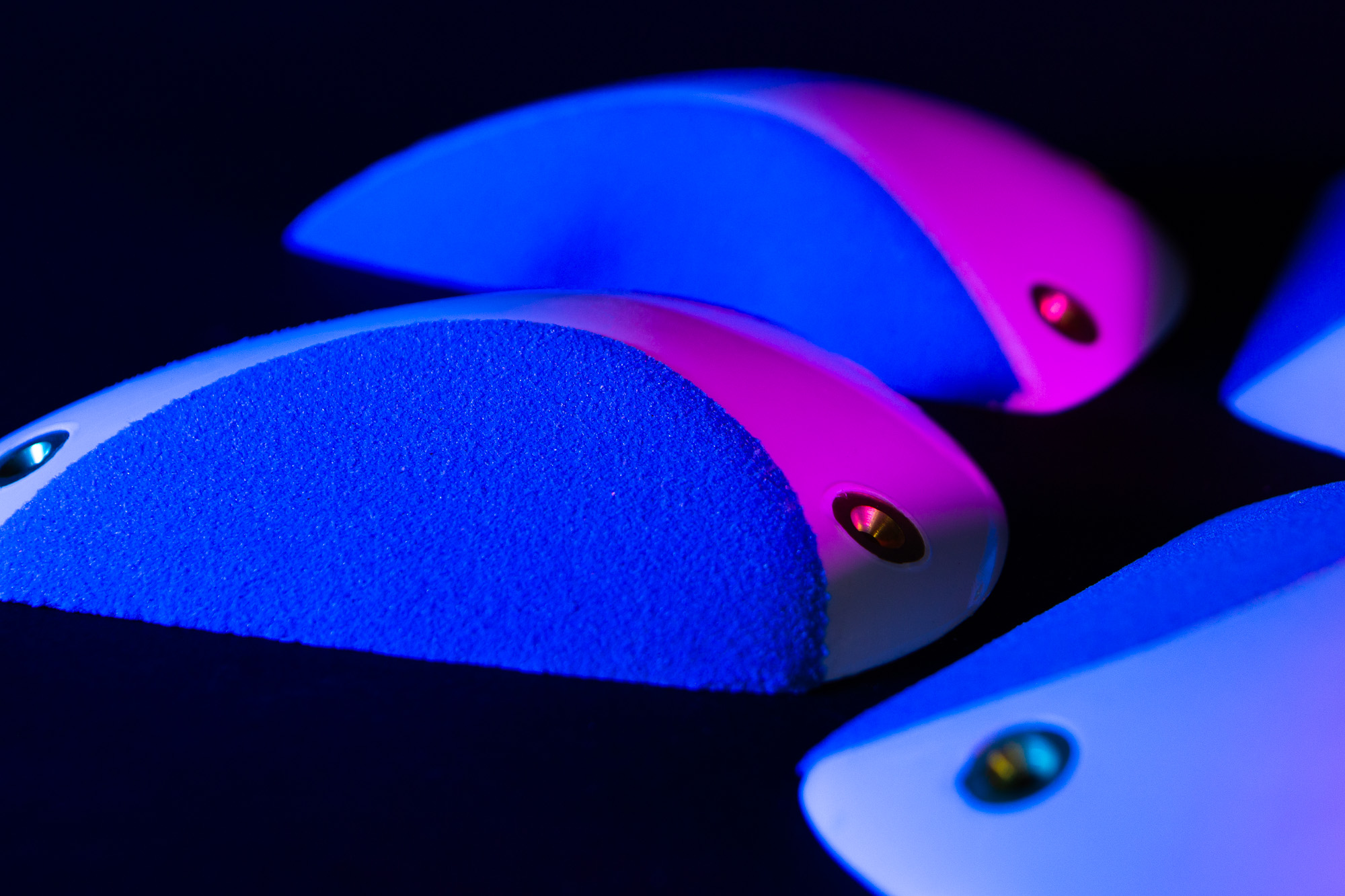
The Future Sustainability of Indoor Climbing
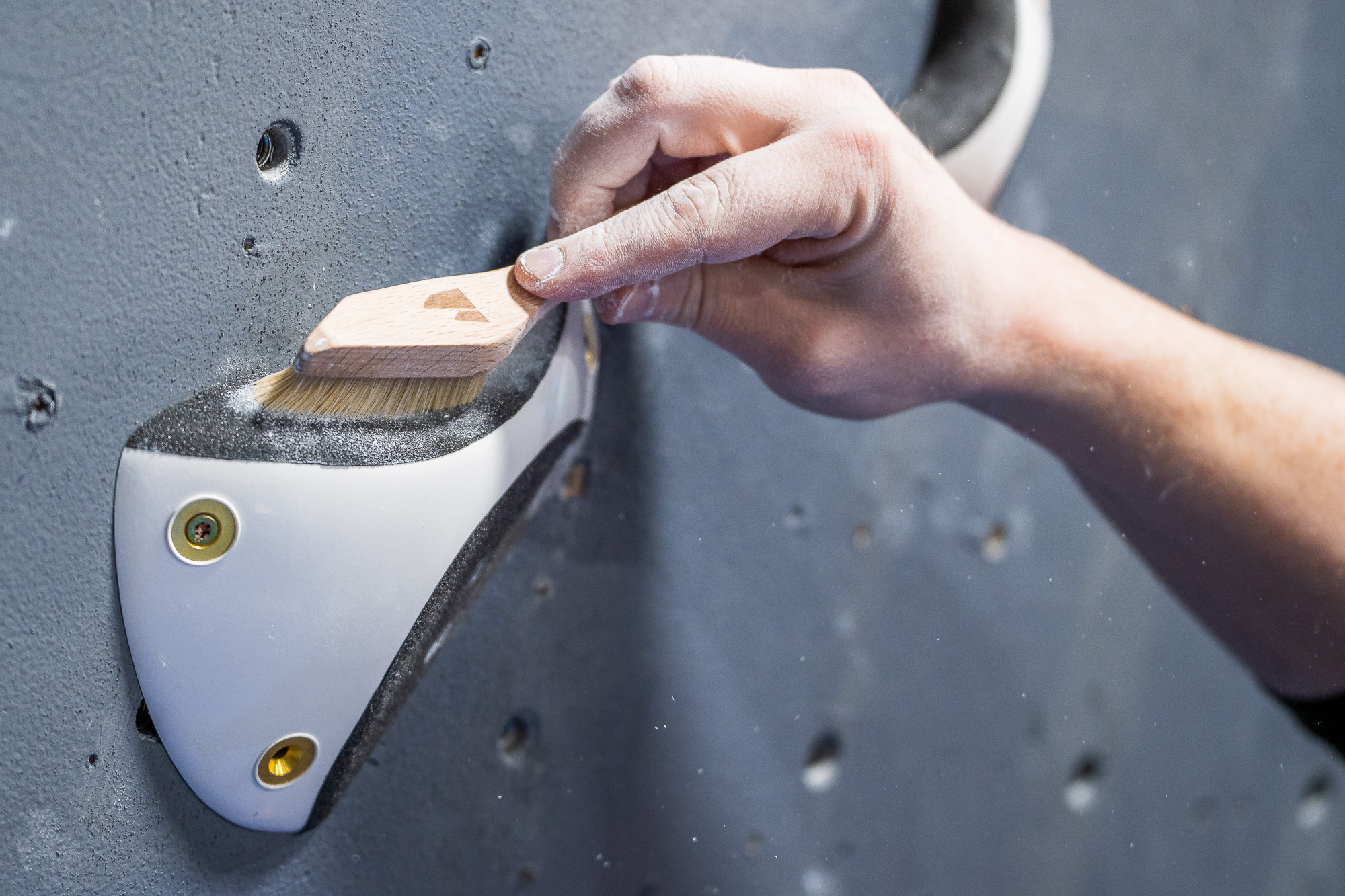