But this wasn’t always the case. In the ’80s and ’90s, steel and aluminum ruled the industry. Titanium was for custom frames or bikes at the tip of the spear. Carbon fiber bike frames were getting going, but the material was still unattainable to most.
Prices have changed interestingly in the last 30+ years of bicycle frame development. Carbon fiber, the rarest frame material of the past, is now common. Although still spendy, the prices have come down.
Steel used to be affordable and still can be. But now, custom builders are getting premium pricing for what used to be the most common frame material. Titanium and aluminum seem to have held their relative position in the frame material pricing hierarchy.
This is our breakdown of the hows and whys of carbon fiber bike frames.
How Carbon Fiber Bike Frames Are Made
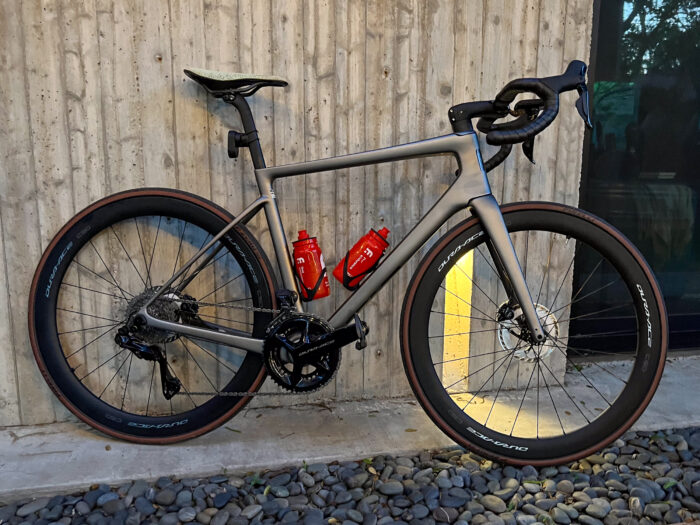
Filaments and Epoxy Resins
Carbon fiber is an excellent material from which to craft a bicycle frame. The strength-to-weight ratio of carbon bike frames is unbeaten, and brands can “program” other characteristics. Manufacturers can alter fiber size and direction, the weaving pattern, if any, the number of layers, the shape of the pieces, and the bonding agent.
Carbon fiber frames start from what it sounds like; thin filaments 10 to 20 times smaller than a human hair. Carbon fabric suppliers group the filaments to form a “tow,” or ribbon. The number of filaments per tow commonly describes carbon in the cycling industry. “3K” carbon has 3,000 filamaments per tow.
Suppliers combine the carbon fiber tows with a bonding agent, usually a two-part epoxy resin. At this stage, the resin and tow are now a composite material the industry calls carbon fiber-reinforced polymer (CFRP).
The carbon filaments alone are incredibly lightweight. The epoxy resin, by contrast, is heavy. So manufacturers do everything they can to limit the amount of resin and any voids within the composite.
The “recipe” of filaments and resin that carbon fiber producers follow affects the “modulus” of the carbon fiber. This term often appears in marketing materials for carbon fiber bike frames and wheels. Modulus refers to the stiffness of the CFRP.
Although it may seem like more stiffness is better, it also means that the carbon fiber has less strength. So, like many aspects of a bicycle, it’s a compromise. Also, higher modulus carbon fiber is more costly to produce.
The carbon fiber fabric usually ships to frame manufacturers in “prepreg” rolls. The carbon fiber supplier impregnates the fabric with epoxy resin, so the frame manufacturer doesn’t have to do that step. The material is ready to be cut into pieces and laid into molds.
At least one brand applies resin to dry carbon fiber fabric draped over wax forms. Other processes, like carbon fiber bike frame printing, are developing.
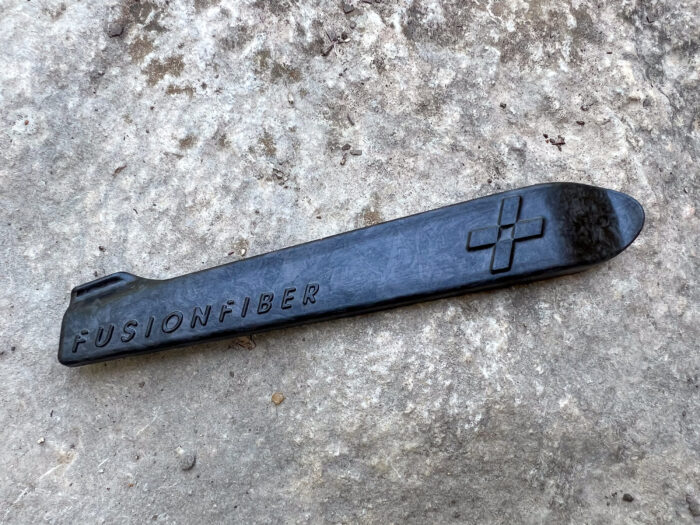
Molds and Layups
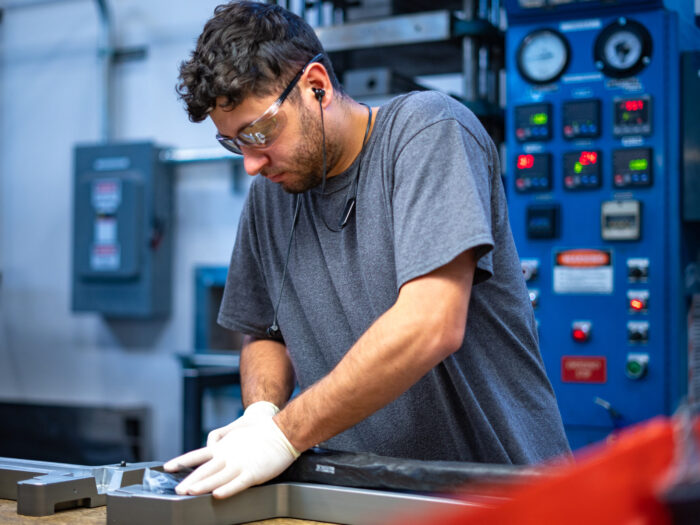
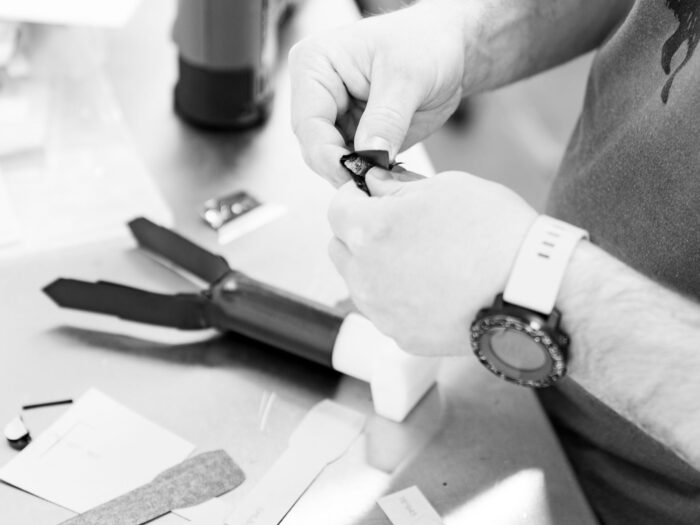
Shake and Bake
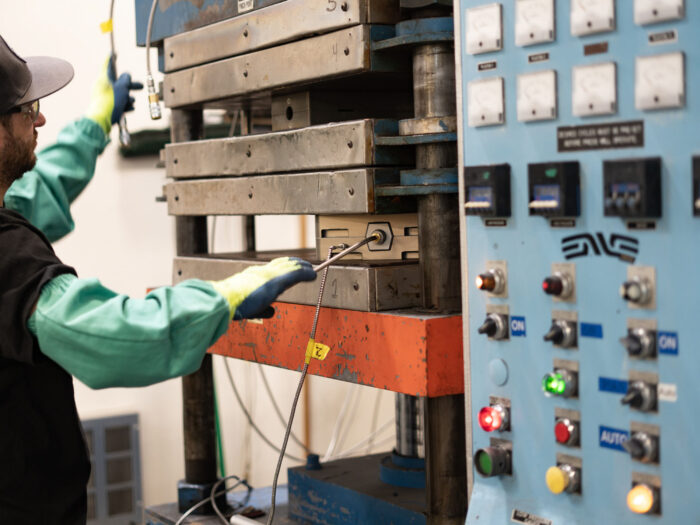
Carbon Bike Frame Post-Mold Processes
The Carbon Fiber Bike Frame Factory Perception
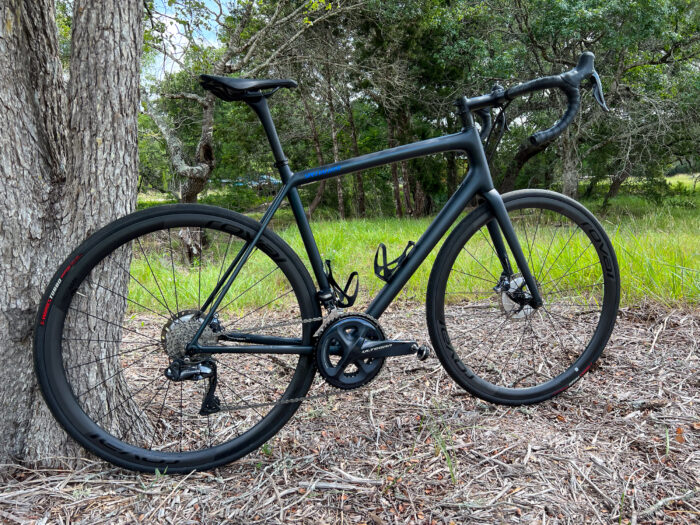
Carbon Fiber Bike Frame: The Most Customizable
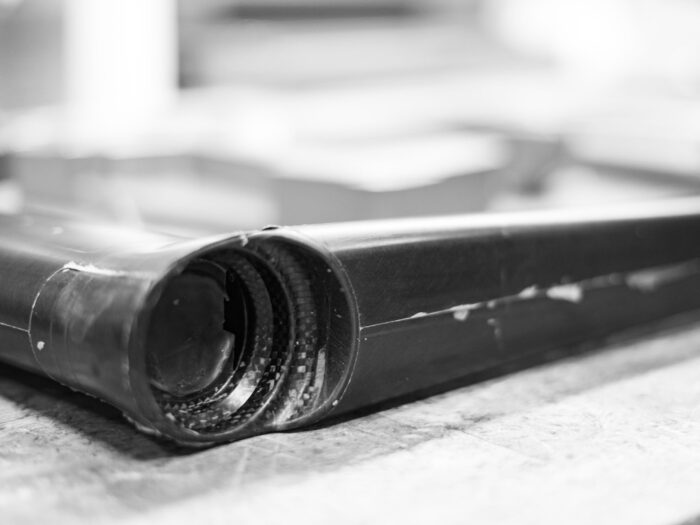