Most polyester products live a single glorious life — as a moisture-wicking shirt, hard-wearing daypack, butt-flattering leggings — before likely making their way to the garbage. There is some recycled polyester, but according to the nonprofit Textile Exchange, 98% of it produced in the world last year did not come from discarded clothes.
Former Under Armour CEO Patrik Frisk said he realized this reality was not sustainable when he was trying to increase the amount of recycled material in clothes across the brand’s product line.
“It was a race to be as ‘recycled’ as possible, without fully understanding the impact of where this whole thing was going,” he told GearJunkie. Collecting bottles to produce more polyester fabric was “not sustainable in the long term,” he said. “I was pretty naive.”
Frisk is now the CEO of Reju, a textile regeneration company owned by French engineering company Technip Industries. On October 3 of this year, Reju announced the opening of its first factory in Frankfurt, Germany, where it plans to produce branded recycled polyester from textile waste that would otherwise be buried, burnt, or dumped.
Then, at the end of last month, Reju announced a three-way partnership between itself, nonprofit thrift store chain Goodwill, and waste management company WM, that will funnel discarded polyester textiles to a future Reju factory based in the U.S.
In an interview with GearJunkie, Frisk said he expects construction on this facility in 2027, and fully operational by 2028.
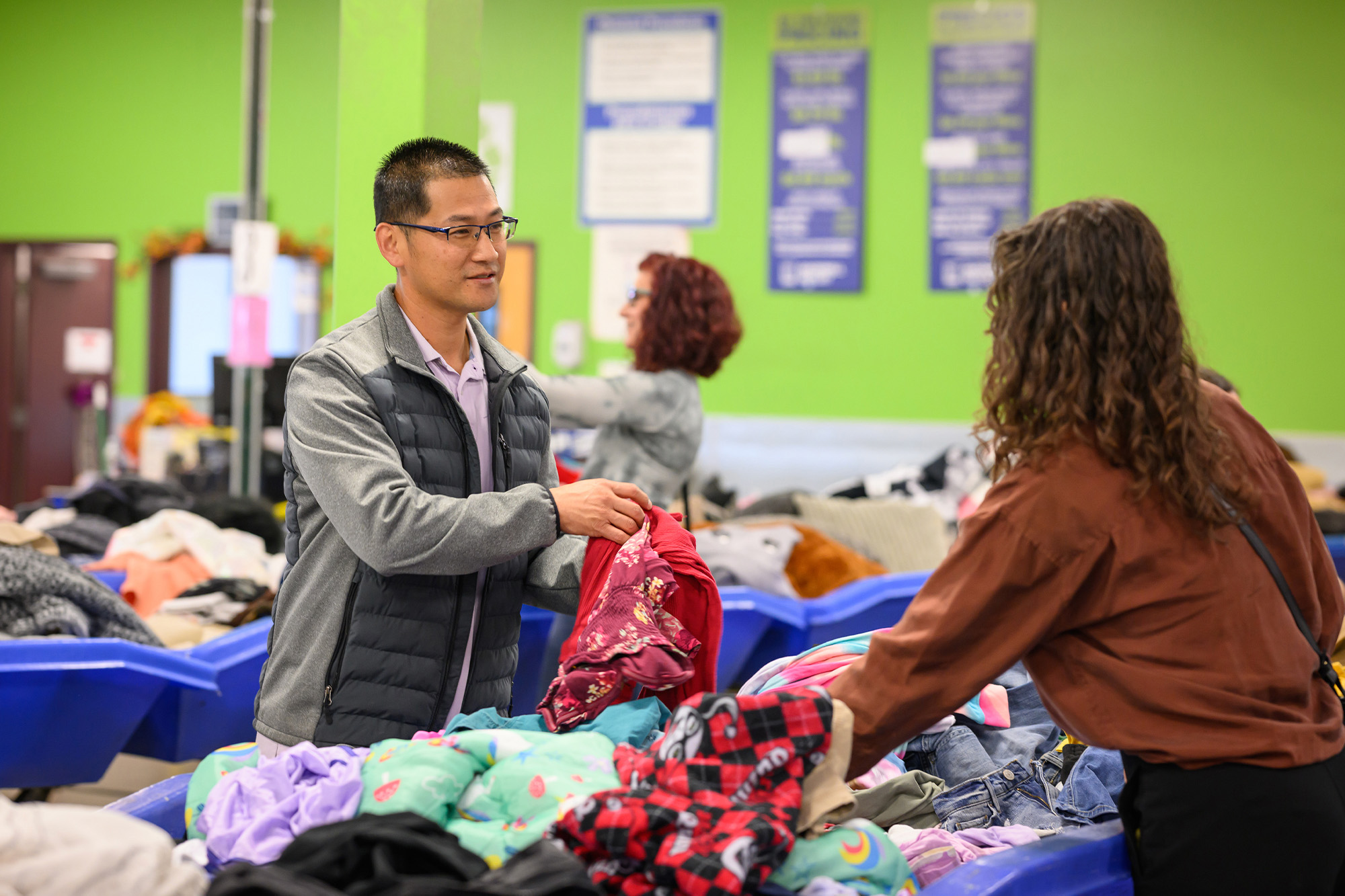
Reju: Recycling Polyester Apparel
Frisk said he hopes Reju will eventually intercept as much of the 92 million tons of textile waste produced each year as possible before it reaches the garbage. This will be made easier in Europe starting next year, when a new rule requires EU member states to establish separate collection systems for used textiles.
Even still, actually turning discarded textiles into Reju polyester requires a significantly different process than producing conventional virgin polyester from petroleum.
“When you use a raw material like textile waste, the challenge is that it comes in many forms,” Frisk said.
In theory, the easiest product for Reju to reclaim is a 100% white polyester shirt. Unfortunately, post-consumer textile waste is a mixture of everything.
“When you start to aggregate textile waste, one of the issues you have is time. You have stuff that’s 40 years old, 20 years old. We’ve gotten better about what we’re putting into textiles … but the reality is, back in the day, things were very nasty.”
The company has developed machines that employ optical and infrared technologies to sort out fabrics made from pure polyester it can reclaim from those made in part from cotton or other materials. Once everything is sorted, the company removes what Frisk refers to as “disruptors,” parts like zippers and buttons.
Then, the material is shredded, removed of any dyes, depolymerized, and reconstituted. Frisk did not confirm if any companies have signed on to use the fabric. He said there are conversations happening, but he wanted to first make it clear to the public that the company had built out its manufacturing capabilities and supply chain.
But, he noted, part of Reju’s appeal will be its capacity to improve on the capabilities of the virgin materials it recycles. According to Frisk, Reju will be able to employ the lessons learned by its parent company to produce better polyester than other commodity manufacturers.
“We take out all the PFAS and other impurities,” Frisk confirmed. “We can create yarns that can be put into fabrics that can be better wicking, softer, more durable … there’s a lot we can do.”